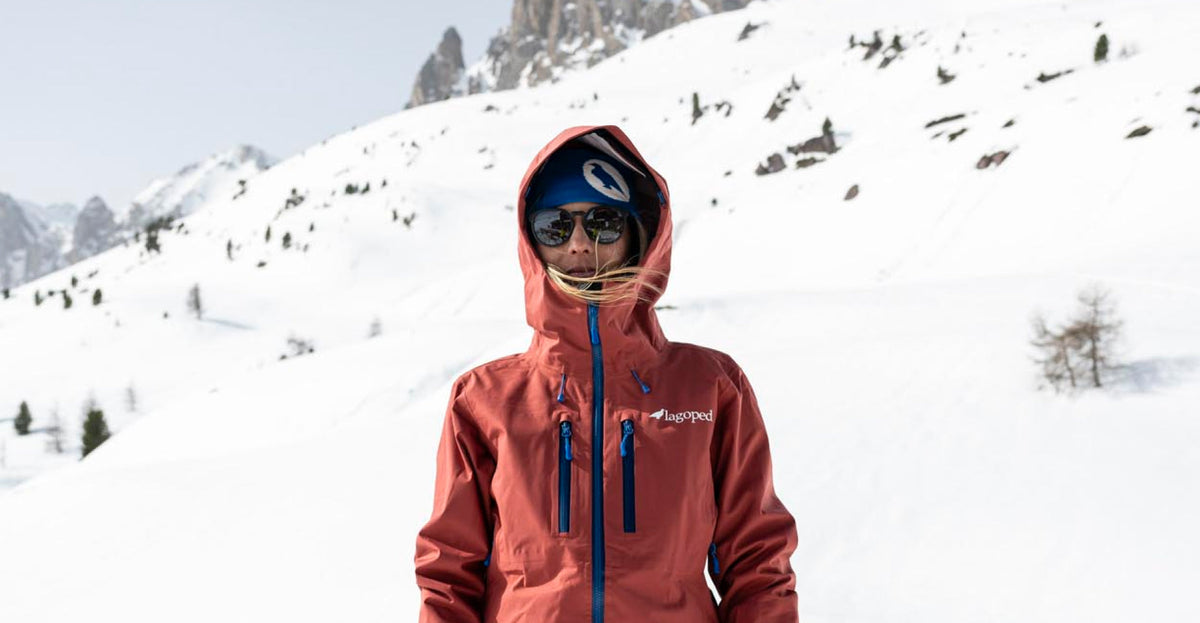
The EVE waterproof jacket: behind the scenes of its eco-responsible manufacturing
|
|
Time to read 10 min
|
|
Time to read 10 min
Since 2018 , the EVE waterproof jacket has been Lagoped's first iconic garment, a symbol of our commitment to designing sustainable and environmentally friendly products. Born from long days spent exploring nature for inspiration, the EVE jacket has evolved over the years thanks to your feedback and the expertise of our product team. Recognizable by its iconic sunny yellow color, it quickly became available in 11 other shades to meet all desires. Made from recycled materials and assembled in Europe, the EVE jacket embodies our vision of responsible fashion, where every manufacturing choice aims to protect nature and leave a positive footprint.
We tell you in detail about the manufacturing process of our waterproof jacket.
Summary
The EVE jacket by Lagoped stands out for its exceptional technical features, which make it an ideal ally for facing the harshest weather conditions. It is waterproof, windproof and breathable , thanks to a waterproof rating of 20,000 Schmerber and seams sealed with heat-sealed tape. Its helmet hood is designed to offer maximum protection without creating entry points for water, snow or wind, while the YKK© Aquaguard zips ensure optimal waterproofing. With a close-fitting cut, slightly longer at the back and elongated sleeves, it offers total freedom of movement , essential for mountain activities. Practical details, such as side vents and cleverly placed pockets, make it a top choice for demanding adventurers.
The name of the EVE jacket at Lagoped is a subtle nod to our commitment to sustainable and responsible fashion. Although it may seem like a first name, EVE is actually a play on words meaning "Finally a recycled jacket made in Europe". This choice of name reflects our mission to create technical clothing from recycled materials, while favoring local production. Other pieces in our collection also have similarly constructed names, always in line with our eco-responsible philosophy. We challenge you to discover these hidden puns in the names of our clothes—can you find them all?
Made with a strong commitment to sustainability, the EVE jacket is made from high-quality recycled materials. The fabric is made of three layers of recycled polyester, including a Sympatex membrane that is also recycled, which ensures optimal breathability and waterproofing. Certified by Oeko-Tex® and its Bluesign® membrane, the jacket is free from substances harmful to health and the environment, such as PTFE and perfluorocarbons, and uses a fluorocarbon-free water-repellent treatment.
The manufacturing of the Lagoped EVE waterproof jacket takes place exclusively in Europe, thus guaranteeing quality and a deep commitment to responsible practices. Each step, from the thread to the fabric to the finalization, is carefully orchestrated in the European Union, avoiding the risks associated with distant productions often marked by human and environmental disasters. By choosing to remain in Europe, Lagoped not only ensures that it benefits from unrivaled textile know-how , since Europe is the cradle of fashion and mountaineering, but also promotes fair social practices by paying each actor in the chain fairly and creating local jobs . This choice also reduces the carbon footprint thanks to closer production and respects strict environmental standards , thus demonstrating a shared responsibility towards nature.
The design of the waterproof jacket at Lagoped begins in the heart of the Venice of the French Alps, in Annecy, where the product team tackles a complex but exciting task. Imagining the jacket means first designing a product that combines technical performance and aesthetics. This creative phase gives rise to detailed sketches and the creation of the pattern , an essential guide for the precise cutting of fabrics.
The process also includes a careful search for materials that meet our strict specifications for functionality, durability and environmental friendliness . Finding the right partners to transform these materials into high-quality finished products is a crucial step, ensuring that each jacket meets our high standards.
Lagoped has chosen to work with the Italian brand Sinterama, which has developed the Newlife™ yarn, a 100% recycled polyester, produced by processing plastic bottles collected in community recycling programs.
Recycling plastic bottles to make polyester yarn is an innovative process that transforms waste into valuable resources. The process begins with collecting and sorting the bottles, which are then cleaned and crushed into flakes. These flakes are melted and extruded to create a continuous yarn of recycled polyester, called Newlife™.
Unlike traditional methods, this mechanical process does not require harsh chemicals or additional dyes, significantly reducing the environmental impact. The yarn produced is not only sustainable, but also of high quality, ensuring garments have a technical performance comparable to that of virgin fibres while contributing to the reduction of plastic waste .
The weaving and dyeing stage of the polyester yarn plays a crucial role in the manufacture of a waterproof jacket. After being transformed into yarn, the recycled polyester is woven to create a strong and resistant fabric, which forms the basis of the jacket. This weaving must be carried out with great precision to guarantee not only the durability of the fabric, but also its waterproofness and breathability, essential for technical clothing. The weaving of the outer layer is carried out in France, in Ardèche, from the NewLife™ yarn. From winter 2024-2025, the weaving of the inner layer is carried out in Italy, from another Italian recycled yarn .
Once the weaving is complete, the fabric is dyed using a rigorous process to ensure high UV resistance , so that the colour remains vibrant even after prolonged exposure to the elements. These weaving and dyeing steps are therefore crucial to ensuring the quality and longevity of waterproof jackets.
The waterproof membrane used in Lagoped jackets is manufactured by Sympatex, a German partner recognized for its commitment to sustainable innovation. This membrane is designed from recycled polyester, including from pre-consumer membrane offcuts , making it a product that is both high-performance and environmentally friendly. Completely free of PTFE and PFC , the Sympatex membrane is not only waterproof, but also breathable and windproof, ensuring optimal protection against bad weather while allowing water vapor to escape. In addition to being 100% recyclable, this membrane meets the highest environmental certifications, such as Bluesign® and Oeko-Tex®, confirming its reduced ecological impact and its safety for health.
The lamination stage is essential in the manufacture of a waterproof jacket, as it consists of assembling the three layers of materials that give the garment its technical properties . This process combines an outer layer of recycled polyester, a waterproof and breathable membrane (such as that of Sympatex), and an inner layer of mesh, also recycled. The lamination is done by fusing the layers under pressure and at high temperature, creating a composite fabric that remains thin while being extremely resistant . This process ensures that the waterproof membrane remains well fixed between the other two layers, guaranteeing effective protection against water and wind, while allowing the evacuation of perspiration. The quality of the lamination is crucial for the durability and performance of the jacket, as it ensures that the layers will not delaminate, even after intense use in extreme conditions.
Applying a water repellent to the laminated fabric of a waterproof jacket is a crucial step in ensuring the garment’s hydrophobic performance. This treatment involves applying a thin layer of water repellent to the outer surface of the fabric, which causes water to bead up instead of absorbing it. This helps maintain the breathability of the laminate while preventing moisture from penetrating through the fibres.
The environmentally conscious Lagoped brand uses a fluorocarbon-free DWR (durable water repellent) finish, avoiding the use of perfluoroalkyl substances (PFAS) often found in conventional water repellent treatments. Since 2008, only environmentally friendly DWRs have been applied to Sympatex products, in line with Lagoped's commitment to sustainable textiles. This innovative approach not only ensures optimal protection against water, but also minimal impact on the environment, thus meeting Lagoped's requirements.
The final step in making a waterproof jacket is assembly, where the individual pieces of laminated fabric are sewn together to form the final garment. This step requires great precision, as each seam potentially creates entry points for water.
To ensure the jacket is completely waterproof, waterproof tapes are applied to all seams. These tapes, usually made of polyurethane, are heat-sealed on the internal seams, thus blocking any infiltration of water or wind. This process is essential to maintain the integrity of the jacket, especially in extreme weather conditions. The final assembly also includes the addition of waterproof zippers and storm flaps, which reinforce the overall protection of the garment.
It is this attention to detail in assembly that ensures the waterproof jacket delivers optimum performance , combining comfort, durability and waterproofness.
The waterproof jacket is then stored in the Alps, waiting to be transported to one of our distributors in France, Switzerland or Belgium, or directly to you!
To extend its lifespan, it may need repair. In this case, we will send it back to Annecy, to our workshop, expert in outdoor repairs, or to a craftsman near you.
At Lagoped, we work every day to make clothes that leave the lightest trace in Nature. We ask ourselves a lot of questions and take up challenges to reduce, reuse, transport less... in summary , to have an eco-design of our products that truly takes into account the overall environmental impact and to validate that we are right to favor “recycled Europe” from thread to garment to get out of the logic of extraction.
We don’t claim to “save the planet”, but we give you all the information about the sincere efforts we are making for responsible manufacturing. That’s why we are proud to be the first brand in Europe to publish the eco-scores of all our garments.
You will see that this has required a lot of energy and work for Lagoped. It is a bit like having the IPCC glasses on your nose to look at your garment. And if we have achieved this with our modest size, we hope that it will be a source of inspiration for the fashion industry.
Lagoped’s EVE jacket stands out with an exceptional eco-score, earning an A according to Peftrust’s assessment. This score reflects remarkable performance across several key criteria. In human health, the jacket excels thanks to the absence of harmful chemicals, ensuring the safety of outdoor sports enthusiasts. In terms of natural resources, the use of recycled materials helps reduce the environmental footprint. In addition, the impact on the ecosystem is minimised thanks to European partners who adhere to strict manufacturing standards. Compared to standard products, Lagoped’s waterproof jacket stands out as the most nature-friendly, offering waterproof protection without compromising on environmental ethics.
To preserve the technical qualities of the EVE waterproof jacket, careful maintenance is essential. It is recommended to machine wash it inside out, at 30°C, closing the zips, and to limit the frequency of washing as well as the quantity of detergent used . Avoid using fabric softener, as the technical fabric does not react well to it. After washing, it is best to air dry the jacket on a hanger or, if necessary, in the dryer for 10 to 15 minutes maximum. It is important to never iron the membrane and to avoid dry cleaning. To maintain water repellency, the application of specific PFC-free sprays is recommended.
In conclusion, the EVE waterproof jacket perfectly embodies Lagoped's commitment to sustainable fashion, respectful of the environment and human health. Thanks to a thoughtful design, using recycled materials and ethical manufacturing, this jacket demonstrates that it is possible to reconcile technical performance and ecological responsibility.
By choosing the EVE waterproof jacket, adventurers are not only opting for optimal protection against the elements, but also making a conscious choice that preserves the planet and supports a more sustainable economy.